Overview
Operational excellence aims to optimize the performance of an organization by continuously improving its processes, systems, and culture. It involves a systematic approach to identifying and eliminating waste, inefficiencies, and defects, while also maximizing value for customers and stakeholders.
Why organizations should thrive for operational excellence?
Operational Excellence integrate different functions of manufacturing with Lean thinking and add a sense of alignment between traditional values and innovation. Operational Excellence consultants underpins the structured yet customized framework to streamline all functions and truly attain the Lean Status.
Key Challenges which we address for our client’s business?
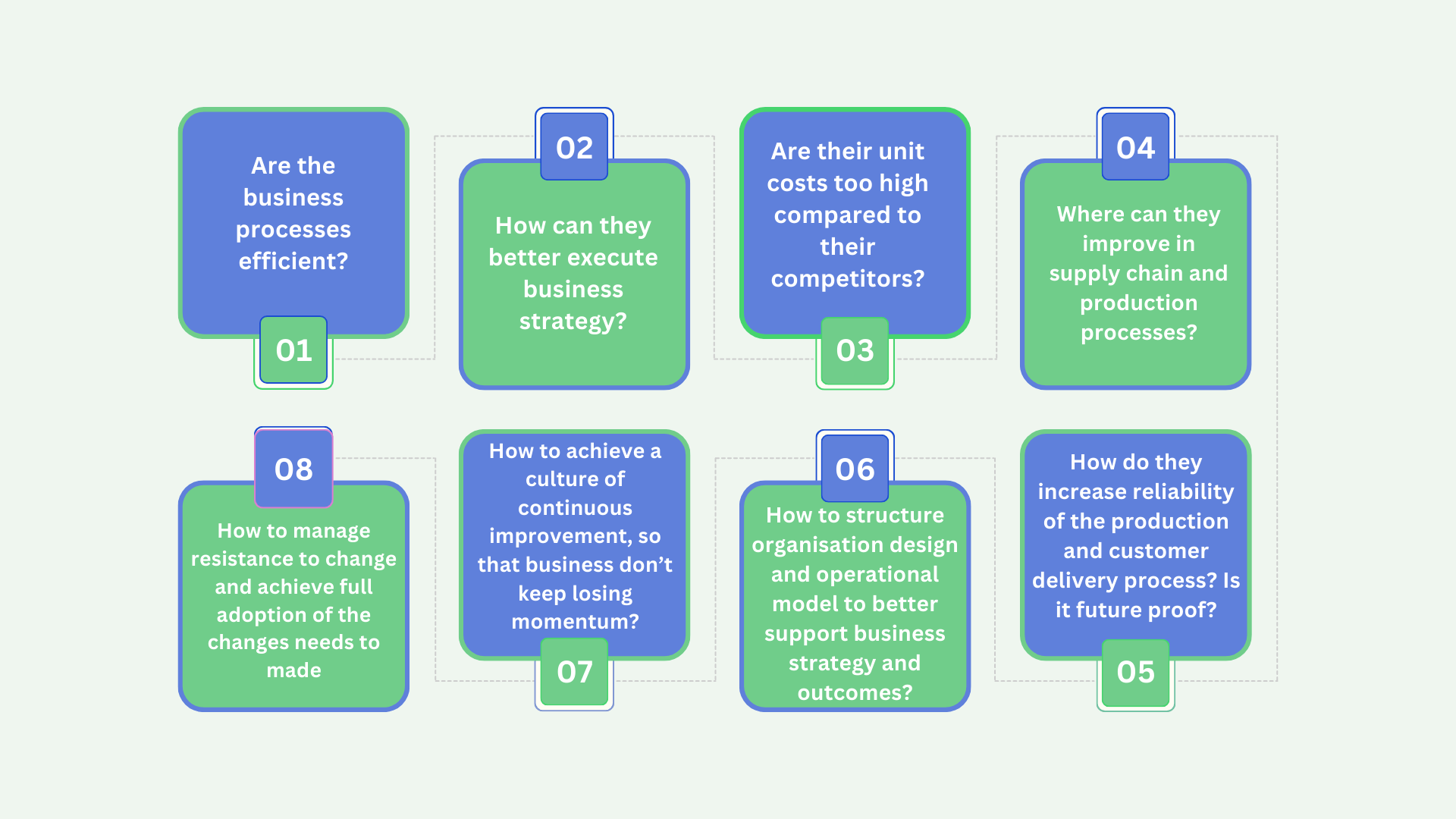
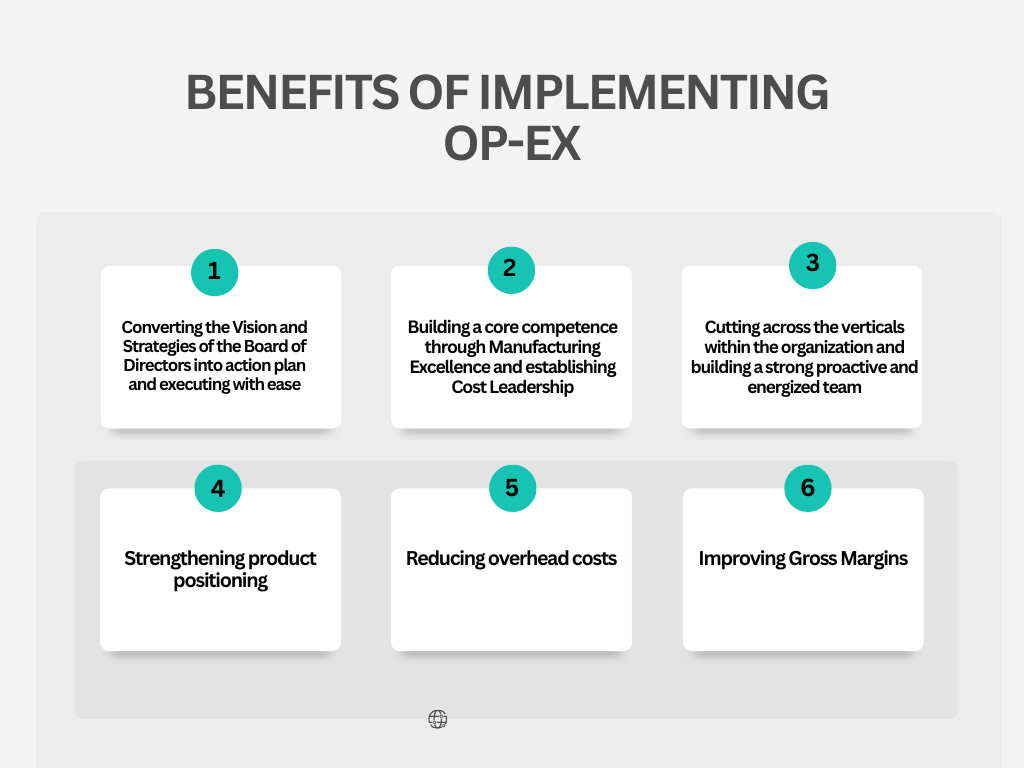
Overview of Lean On Us (LOU)
Integrated Op-Ex Model
- To build the expertise of our own teams and to better support our clients, we established a competence center: Lean On Us (LOU) Integrated Op-Ex Model
- This Model identifies and captures opportunities for organizations to grow, whether by reallocating resources to free up capital for investment, finding new sources of competitive advantage, or fully optimizing portfolios of products and services. It is the thoughtful application of new technologies and capabilities that drives productivity throughout the organization and across the entire value chain, from product development and procurement to manufacturing and the supply chain to service operations to capital excellence.
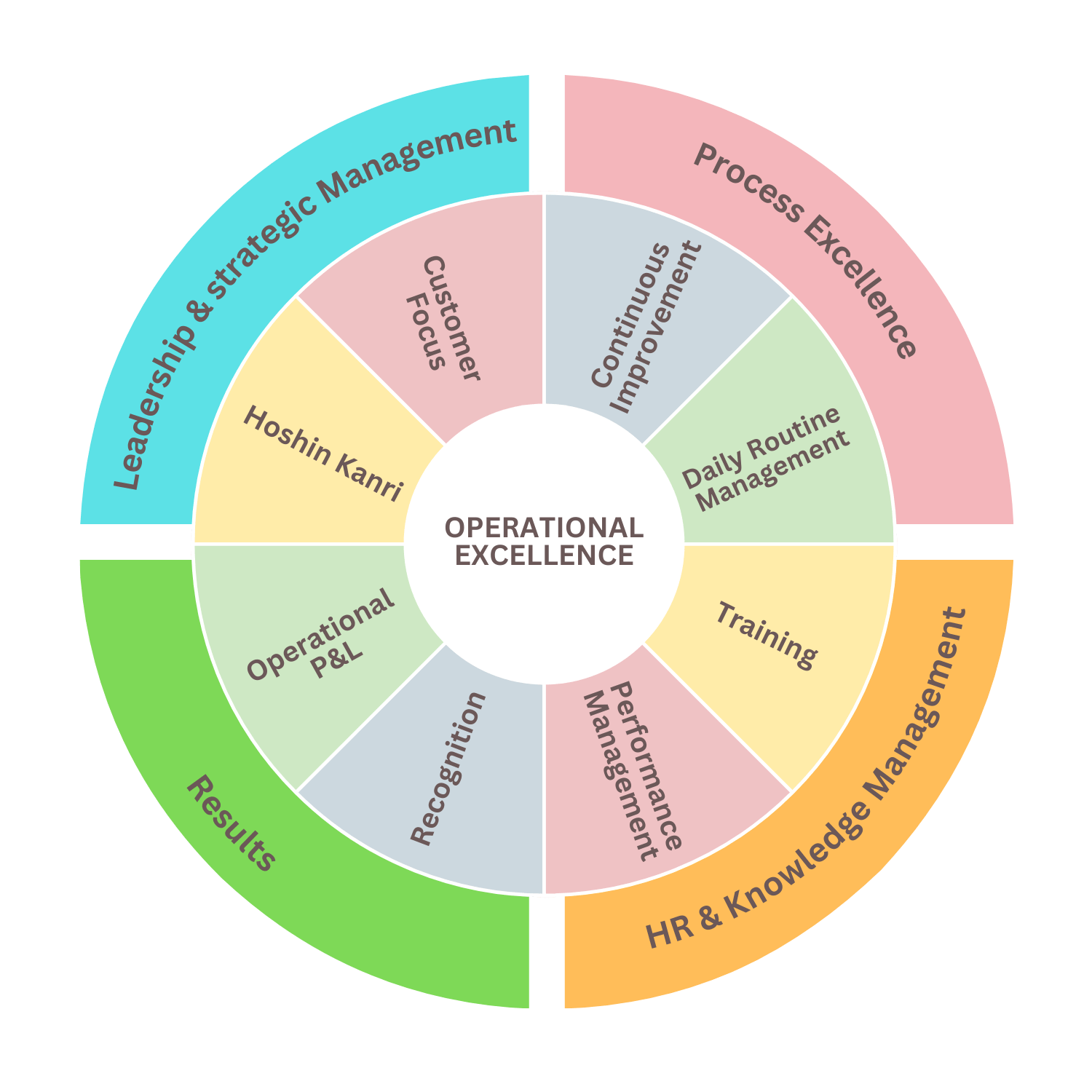
Elements of Operational Excellence
Process
Processes makes us to understand that the business is only as good as the processes within it. Process Excellence is concerned with making processes more efficient and effective through design and testing
People
- It is the People Who Contribute to Operational Excellence.
- Management should invest on training by creating a healthy and competitive culture as well as an attitude in the company that encourages people to strive for excellence. Operational excellence is achieved through standardization of processes, automation, training and retraining the employees
Strategic excellence
Strategy
- Most companies still face the tragedy of a strategy delivering no results with common obstructions, including ineffective processes, poor formulation, and poor execution. To succeed, leaders must carefully overcome these roadblocks and find the vital few initiatives to transform their businesses.
- From the boardroom to the shop floor, we can help you improve every facet of your strategy, tailoring an approach that scales from targeted enhancements to a complete reinvention of your capabilities. We guide organizations by building their path for business sustainable growth via a premium strategy planning and execution framework, striving to achieve stretch goals.
Strategic Planning
- Identify and select the vital few strategic business imperatives.
- Select 3 to 5-year priorities that will drive the organization to sustained profitable growth.
- Set a one-page plan to grow your core business and explore expansion.
Strategy Deployment
- Transform 3 to 5-year imperatives into key capabilities to be implemented at all organizational levels.
- Assign owners to breakthrough priorities.
- Communicate and engage all stakeholders in the same simple and elegant strategic vision.
Breakthrough Priorities
- “Make things happen” approach strategy execution in a practical way.
- Check TTI (Targets To Improve) regularly.
- React to gaps with top management problem-solving.
Strategy Review
- Reflect and learn from strategy execution hazards.
- Launch a new strategy cycle based on lessons learned and change drivers.
Lean Manufacturing Tools
There are several tools and techniques commonly used in Lean Manufacturing to identify and eliminate waste, streamline processes, and improve overall efficiency.
- Value Stream Mapping (VSM): A visual tool used to analyze and optimize the flow of materials and information in a process or value stream, identifying value-added and non-value-added activities.
- Kaizen: A continuous improvement approach that encourages small, incremental changes in processes and fosters a culture of continuous learning and improvement.
- 5S:A workplace organization method involving sorting, setting in order, shining, standardizing, and sustaining, to create a clean, organized, and efficient work environment.
- Kanban:A visual management tool using signals to control the flow of work and materials, preventing overproduction, minimizing inventory, and improving flow.
- Poka-Yoke: Designing processes or tools to prevent errors or mistakes from occurring, reducing defects and rework.
- Just-in-Time (JIT): Producing items only when they are needed, in the quantities needed, and in the sequence needed, to reduce inventory and lead times.
- Standard Work: Documenting the best-known way to perform a task, training employees, and continuously improving the standard to ensure consistency and quality.
- Total Productive Maintenance (TPM): Involving all employees in equipment maintenance and improvement to minimize downtime, improve reliability, and extend equipment life.
- Continuous Flow:Organizing work to minimize interruptions and delays, and ensure smooth flow through the process, reducing lead times and improving efficiency.
- Root Cause Analysis (RCA): Identifying and addressing the underlying causes of problems, rather than just treating symptoms, to prevent recurrence.
- Andon: Visual management tool that alerts to abnormal conditions in the process, enabling quick response and problem-solving.
- Heijunka (Production Leveling): Leveling the production workload to achieve a consistent and predictable flow of work, improving efficiency and reducing waste.
- Single-Minute Exchange of Die (SMED): Reducing changeover time in equipment to minimize downtime and increase flexibility.
- Visual Management: Using visual tools and techniques to communicate information, monitor performance, and drive improvement.
- Gemba Walks: Going to the actual work area to observe, engage, and understand the process, enabling better decision-making and problem-solving.
- Takt Time: Calculating the rate at which products or services need to be produced to meet customer demand, providing a basis for production planning and scheduling.
- Cycle Time Reduction: Analyzing and reducing the time required to complete a process or activity, improving productivity and efficiency.
- Pull Systems: Establishing systems where work is pulled based on actual customer demand, minimizing overproduction and inventory.
- Cellular Manufacturing: Organizing work areas into self-contained cells to reduce movement, improve flow, and increase flexibility.
- OEE (Overall Equipment Efficiency): A measure of equipment performance that takes into account availability, performance, and quality, providing insights into equipment effectiveness and identifying improvement opportunities.
- Quick Changeover: Reducing the time required to change from one product or process to another, minimizing downtime and increasing flexibility.
- Waste Reduction (TIMWOOD): Identifying and eliminating the seven common forms of waste: Transportation, Inventory, Motion, Waiting, Overproduction, Over-processing, and Defects.
- Process Flow Analysis: Analyzing and optimizing the flow of work through a process, identifying bottlenecks and constraints, and improving flow.
- Error-Proofing (Poka-Yoke): Designing processes or tools to prevent errors or mistakes from occurring, reducing defects and rework.
- A3 Problem Solving: Using a structured problem-solving approach on a single sheet of paper (A3 size) to identify
Six Sigma
- Six Sigma ranks among the foremost methodologies for making business processes more effective and efficient. In addition to establishing a culture dedicated to continuous process improvement, Six Sigma techniques reduce variance and help identify the root causes of errors, allowing organizations to create better products and services for consumers.
- While most people associate Six Sigma with manufacturing, the methodology is applicable to every type of process in any industry. In all settings, organizations use Six Sigma to set up a management system that systematically identifies errors and provides methods for eliminating them.
Six Sigma Methodology
DMAIC
- Define the problem and the project goals
- Measure in detail the various aspects of the current process
- Analyze data to, among other things, find the root defects in a process
- Improve the process
- Control how the process is done in the future
Lean Six Sigma Training
1-Lean Manufacturing Basics
2-Lean Six Sigma Yellow Belt Training
3-Lean Six Sigma Green Belt Training